Aero Mould: Your Premier Choice for Bicolor Injection Molding Solutions
In the dynamic realm of plastic manufacturing, the demand for innovative and high - quality solutions is ever - growing. Among the various molding techniques, bicolor injection molding has emerged as a game - changer, allowing for the creation of products with enhanced aesthetics and functionality. At Aero Mould, we have positioned ourselves as a leading professional in the production of bicolor injection molds, bringing a wealth of experience and cutting - edge technology to every project.
1. Our Expertise in Bicolor Injection Molds
Bicolor injection molding is a complex process that involves injecting two different materials or colors into a single mold in two distinct steps. This results in a single, integrated product with unique visual and tactile properties. Aero Mould has mastered this intricate process, with a team of highly skilled engineers and technicians who have in - depth knowledge of bicolor mold design and manufacturing.
1.1 Customized Design
We understand that each customer's product is unique, and thus, requires a tailored mold design. Our design team works closely with clients from the initial concept stage. Using state - of - the - art 3D design software such as UG, Pro - E, we create detailed and precise mold designs. Whether it's a small consumer product or a large industrial component, we ensure that the mold design meets the specific requirements of the product, including dimensions, functionality, and aesthetic appeal.
For example, if a client needs a bicolor plastic handle for a tool, our designers will consider factors such as the ergonomics of the handle, the compatibility of the two materials (for a comfortable grip and durability), and the visual contrast between the two colors to make the product stand out in the market.
1.2 Advanced Manufacturing Technology
Aero Mould is equipped with the latest manufacturing equipment to bring our designs to life with the highest precision. We utilize Computer Numerical Control (CNC) machining centers, Electrical Discharge Machining (EDM) equipment, and high - speed milling machines. These advanced tools enable us to achieve tight tolerances and intricate details in our bicolor molds.
Our CNC machining centers can precisely cut and shape the mold components, ensuring that the two cavities for the different materials are perfectly aligned. EDM is used for creating complex geometries and fine - tuned features that are difficult to achieve through traditional machining methods. This combination of technologies allows us to produce molds that can consistently deliver high - quality bicolor products with excellent surface finishes.
2. The Process of Bicolor Injection Molding at Aero Mould
2.1 Mold Design and Development
The first step in our bicolor injection molding process is the comprehensive mold design. As mentioned earlier, our design team collaborates with clients to understand their product requirements. Once the design is finalized, we move on to the development phase.
We use high - quality mold steels and other materials to ensure the durability and longevity of the mold. The mold is designed in such a way that the two - shot injection process can be carried out smoothly. This includes proper positioning of the gates for each material, efficient cooling channels to ensure even cooling of the two materials, and a robust locking mechanism to prevent any misalignment during the injection process.
2.2 Material Selection and Preparation
Selecting the right materials is crucial for the success of a bicolor injection molding project. We work with a wide range of plastic materials, including ABS, PP, PC, and TPE, depending on the product's application and performance requirements. Our team of material experts can provide valuable advice on material selection, taking into account factors such as strength, flexibility, heat resistance, and color compatibility.
Before the injection process, the materials are carefully dried and prepared to remove any moisture or impurities. This ensures that the final product has the desired quality and mechanical properties.
2.3 Injection Molding Process
In the injection molding stage, the prepared materials are fed into the injection molding machine. The machine injects the first material into the mold cavity, where it cools and solidifies. Then, the mold rotates or moves in a precise manner, and the second material is injected, bonding with the first material to form the final bicolor product. Aero Mould's injection molding machines are equipped with advanced control systems that allow for precise control of injection pressure, temperature, and injection speed. This ensures consistent quality from one product to another and minimizes the occurrence of defects such as warping, shrinkage, or poor adhesion between the two materials.
2.4 Quality Control and Inspection
Quality is at the heart of everything we do at Aero Mould. We have a rigorous quality control system in place that starts from the raw material inspection and continues throughout the entire manufacturing process. After the bicolor products are molded, they undergo a series of inspections, including dimensional checks, visual inspections for surface defects, and functional tests.
We use advanced measuring equipment such as coordinate measuring machines (CMM) to ensure that the products meet the exact specifications. Any products that do not meet our high - quality standards are either reworked or discarded, guaranteeing that our clients receive only the best - quality bicolor products.
3. Applications of Our Bicolor Injection Molds
Our bicolor injection molds find applications in a wide range of industries:
3.1 Consumer Goods
In the consumer goods industry, our molds are used to produce products such as kitchen utensils, household appliances, and personal care products. For example, a bicolor toothbrush with a soft bristled section and a colored, ergonomic handle can be produced using our molds. The two - color design not only makes the product more visually appealing but also enhances its functionality.
3.2 Automotive Industry
In the automotive sector, bicolor injection molding is used for interior components such as dashboard panels, door handles, and steering wheel grips. These components require a combination of aesthetics, durability, and comfort. Our molds can produce parts with different textures and colors, meeting the high - end requirements of the automotive industry.
3.3 Electronics
For electronic devices, bicolor injection molding is often used for the production of device housings, buttons, and other components. The ability to combine different colors and materials in a single part can improve the overall look and feel of the electronic product, making it more attractive to consumers.
4. Why Choose Aero Mould?
4.1 Experience and Reputation
With years of experience in the mold - making industry, Aero Mould has built a solid reputation for delivering high - quality bicolor injection molds and products. Our long - standing relationships with clients from various industries are a testament to our commitment to excellence.
4.2 Technical Expertise
Our team of engineers and technicians is highly trained and experienced in all aspects of bicolor injection molding. We stay updated with the latest industry trends and technologies, allowing us to offer innovative solutions to our clients.
4.3 Quality Assurance
We adhere to strict quality control measures at every stage of the production process. From the design and manufacturing of the molds to the final inspection of the products, we ensure that everything meets the highest quality standards.
4.4 Customer Service
At Aero Mould, we believe in providing exceptional customer service. We work closely with our clients, keeping them informed throughout the project and addressing any concerns or questions promptly. Our goal is to not only meet but exceed our clients' expectations.
In conclusion, if you are looking for a reliable partner for your bicolor injection molding needs, Aero Mould is the answer. With our expertise, advanced technology, and commitment to quality, we can help you bring your innovative product ideas to life. Contact us today to discuss your project requirements and let us show you how we can make a difference in your plastic manufacturing endeavors.
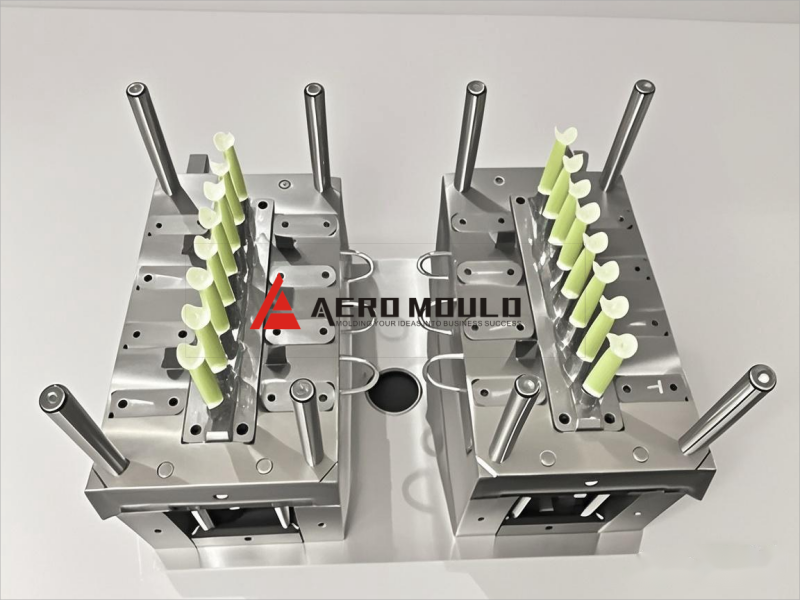
Outline:
1. Introduction to Aero Mould and its products
2. The company's target market and benefits of using their products
3. Description of thin wall, cap, and bi-material moulds
4. Advantages of using Aero Mould's products
5. Customer satisfaction and feedback
6. Conclusion
Aero Mould is a leading manufacturer of premium quality thin wall, cap, and bi-material moulds. The company is known for producing high-performance moulds that are designed to meet the needs of various industries. Aero Mould's products are highly sought after in North America, Europe, and Russia.
Thin wall moulds are designed to produce thin-walled containers such as food packaging, disposable cups, and containers. The moulds are manufactured with high precision and accuracy to ensure that they meet the desired specifications. Cap moulds, on the other hand, are designed to produce caps and closures for various products such as beverages, cosmetics, and pharmaceuticals. These moulds are manufactured using high-quality materials to ensure durability and excellent performance.
Bi-material moulds are used to produce products that require two or more materials to be fused together. These moulds are designed with advanced technology that allows for the perfect fusion of different materials, resulting in exceptional product quality. Aero Mould's bi-material moulds are known for their high precision and accuracy, making them ideal for producing complex products.
The use of Aero Mould's products offers numerous benefits to clients. The moulds have a fast cycle time and a long lifespan, which ensures that clients minimize their production costs. With Aero Mould's products, clients can produce high-quality products that meet the highest standards of the industry.
Aero Mould's commitment to quality and customer satisfaction has earned them high praise from their clients. The company has a team of experienced professionals who are dedicated to producing the best quality products that meet the needs of their clients.
In conclusion, Aero Mould is a reliable and reputable manufacturer of thin wall, cap, and bi-material moulds. The company's commitment to quality, innovation, and customer satisfaction makes them stand out in the industry. With Aero Mould's products, clients can be assured of high-quality and long-lasting moulds that are designed to meet their specific needs.
Outline:
1. Introduction to Aero Mould and its products
2. The company's target market and benefits of using their products
3. Description of thin wall, cap, and bi-material moulds
4. Advantages of using Aero Mould's products
5. Customer satisfaction and feedback
6. Conclusion
Content:
Aero Mould is a leading manufacturer of premium quality thin wall, cap, and bi-material moulds. The company is known for producing high-performance moulds that are designed to meet the needs of various industries. Aero Mould's products are highly sought after in North America, Europe, and Russia.
Thin wall moulds are designed to produce thin-walled containers such as food packaging, disposable cups, and containers. The moulds are manufactured with high precision and accuracy to ensure that they meet the desired specifications. Cap moulds, on the other hand, are designed to produce caps and closures for various products such as beverages, cosmetics, and pharmaceuticals. These moulds are manufactured using high-quality materials to ensure durability and excellent performance.
Bi-material moulds are used to produce products that require two or more materials to be fused together. These moulds are designed with advanced technology that allows for the perfect fusion of different materials, resulting in exceptional product quality. Aero Mould's bi-material moulds are known for their high precision and accuracy, making them ideal for producing complex products.
The use of Aero Mould's products offers numerous benefits to clients. The moulds have a fast cycle time and a long lifespan, which ensures that clients minimize their production costs. With Aero Mould's products, clients can produce high-quality products that meet the highest standards of the industry.
Aero Mould's commitment to quality and customer satisfaction has earned them high praise from their clients. The company has a team of experienced professionals who are dedicated to producing the best quality products that meet the needs of their clients.
In conclusion, Aero Mould is a reliable and reputable manufacturer of thin wall, cap, and bi-material moulds. The company's commitment to quality, innovation, and customer satisfaction makes them stand out in the industry. With Aero Mould's products, clients can be assured of high-quality and long-lasting moulds that are designed to meet their specific needs.
AERO MOULD, as a leading manufacturer of various types of moulds. Located in Taizhou, Zhejiang, we specialize in producing top-notch moulds for a wide range of industries. At AERO MOULD, we take pride in our expertise in crafting moulds for sports bottle caps, aerosol caps, pharmacuetical caps, cosmetic caps, and more.
With years of experience and a dedicated team of professionals, we ensure that our moulds meet the highest standards of quality and precision.
Why choose AERO MOULD as your mould supplier? Here are a few reasons:
1. Superior Quality: Our moulds are made using the finest materials and cutting-edge technology, guaranteeing durability and longevity.
2. Customization: We understand that every client has unique requirements. Hence, we offer tailored solutions to meet your specific needs, ensuring complete customer satisfaction.
3. Competitive Pricing: We believe in providing value for money. Our moulds are competitively priced without compromising on quality, making us a cost-effective choice for your business.
4. Timely Delivery: We understand the importance of timely production and delivery. With our streamlined processes, we ensure prompt delivery of your orders, saving you time and hassle.
5. Excellent Customer Support: Our dedicated customer support team is always ready to assist you with any queries or concerns. We strive to build long-term relationships with our clients by providing exceptional service.
We would be delighted to discuss your mould requirements and provide you with a customized solution. Please feel free to reach out to us at quotation@aeromoulds.com for more information. Thank you for considering AERO MOULD as your trusted partner for high-quality cap moulds. We look forward to the opportunity of serving you.
We are excited to introduce our latest thin wall mould, the 4-Cavity Thin-Wall Flower Pot Mould, designed to revolutionize your production process and enhance your efficiency.
At Aero Mould, we understand the importance of speed and quality in today's competitive market. That's why our mould is engineered to deliver exceptional results with a remarkable molding cycle of just 6-8 seconds. This means you can produce more flower pots in less time, giving you a significant advantage over your competitors.
Our 4-Cavity Thin-Wall Flower Pot Mould is meticulously crafted using advanced tooling equipments and high-quality materials, ensuring durability and precision. Its innovative design allows for seamless demolding, increasing your overall productivity.
We believe that investing in our mould will not only streamline your production process but also help you meet the growing demand for high-quality flower pots. With our mould, you can create stunning, lightweight, and durable flower pots that will captivate your customers and set your brand apart.
Don't miss out on this opportunity to take your production to the next level. Contact us today to learn more about our 4-Cavity Thin-Wall Flower Pot Mould and how it can benefit your business.
Thank you for considering AERO as your trusted partner. We look forward to hearing from you soon.
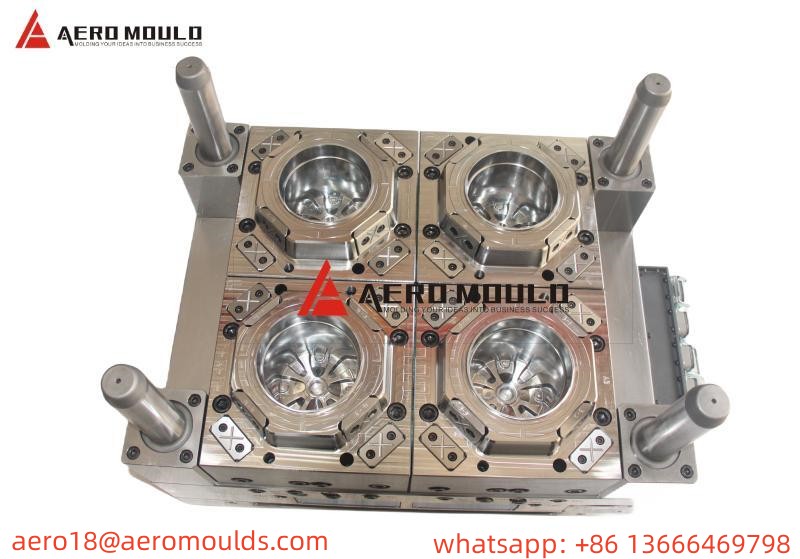
The development and maturity of bi-material injection molding technology have made plastic products increasingly beautiful. More and more molding companies are developing bi-color products. Our company has over 15 years of experience in making two-shots moulds, specializing in the production of bi-material molds for caps and housewares, etc.
Aero Mould is a comprehensive injection mold manufacturer located in 18# KaiTuo Road, XinQian Street, Huangyan Taizhou China. We specialized in making all types of cap molds for pharmaceutical, food packaging, cosmetics, chemical industries, etc. We have very rich experience in making flip-top caps, disc cap, pouch cap & spout, shaker bottle cap, aerosol cap, etc.
Steel S136, DC53 and other materials with good stability used for mold core and cavity, P20H and 4CR13H used for the mould base. And the mould life can be 3-5 million shots.
When we make a multi-cavity mould, the cooling effect is the most important thing. The shorter cycle time the more output. So we have to make optimal cooling design, make the cooling maximum close to the molding area but not affect the mold strength. And sometimes the fastcool steel will be adopted on the core and cavity. So our customer are always very happy with our mold cooling.
Chinaplas is currently the largest rubber and plastic exhibition in China and even in the world. CHINAPLAS 2023 will be held at the Shenzhen World Exhibition and Convention Center from April 17th to 20th.
As a professional high-quality mold manufacturer, Aero Mold will also participate in 2023 CHINAPLAS, booth number 7S17. At that time, we will exhibit some medical caps, flip-top shampoo cap, cosmetic cap, sports water bottle lids, thin wall containers, disposable products, etc.
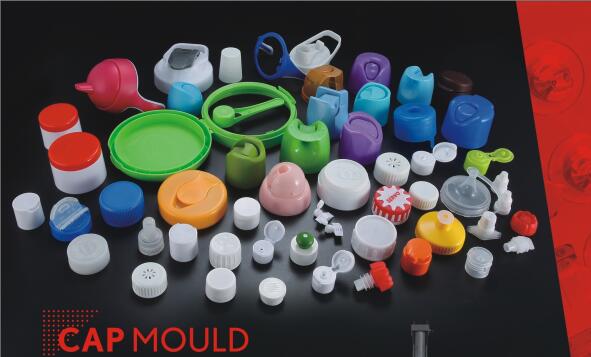
Aero Mould Co.,Ltd is a professional large mold making factory located in Taizhou, China. We specialized in making the large oil tank lid mould, bath tub moulds, industrial moulds, etc.
With the outbreak of new coronaviruses worldwide, the demand for hand sanitizers and disinfectants has also peaked. Aero Mould is a Chinese mould factory who are specialized in making various of cap moulds, We have strong faith that our quality will help your business grow. We are making 20/410, 24/410 and 28/410 hand sanitizer cap mould for our customers.
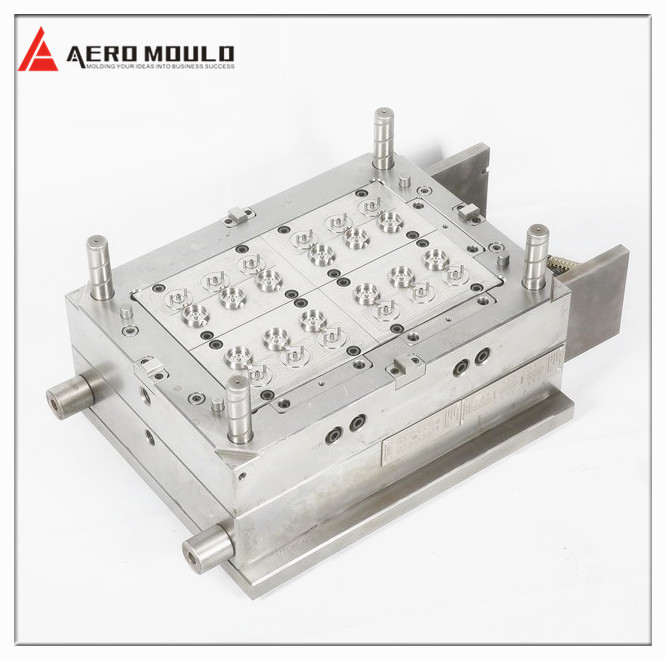
“Thin wall” usually refers to products with a wall thickness of less than 1 mm. Thin-walled products require changes in the process: higher pressures and speeds, shorter cooling times, and changes in the ejector and gate arrangement of the parts. Changes in processing technology have further contributed to the development of molds, machines and parts.
Aero Mould Co.,Ltd has rich experience in design and manufacture thin wall moulds, like thin wall container mold, mold for thin wall disposable ware, thin wall mould for IML projects, etc. We always believe a good mold design can greatly increase our customers' production. When our designer making the design for every project, the first thing he considered is the cooling time. He will try every possible to make cooling to everywhere of the part, so can greatly bring down the cooling time and immediately increase the output.
Regarding the mould steel:
-
considering the high speed and high pressure injection, and the mold need to connect chilled water, we always use stainless steel 2316 for the base
-
core & cavity steel: considering to be anti-rust and long mould life requirment, we always use 2344 HRC48-52, S136 HRC48-52, DC53 HRC48-52, etc
Two-color injection molding refers to the injection molding of two different materials into the same set of molds, so that the injection molded parts are formed by two materials. Some of the two materials are different colors, and some are soft and hard, which improves the product's aesthetics and assembly performance.
Double-shot molding is a method in which two plastics of the same color are plasticized through two barrels, either simultaneously or sequentially through the same nozzle. By using two injection molding machines or two-color injection molding machines, various kinds of mixed color patterns can be obtained, and products with obvious color separation can also be obtained.
Aero Mould Co.,Ltd is a professional and experienced
double color mould making factory in China, we have made more than 30 sets two color moulds in the year of 2018. Below is an example of the two color mold we made.
product name: two color mop cap mould
product material: PP + TPR
product weight: 40 grams
mould cavity: 4+4
mould steel: H13 HRC45-48
mould size: 550*580*660mm
mould running: fully automatically